The JAM-5200EBM Development Trajectory - The future of electron beam metal 3D printers
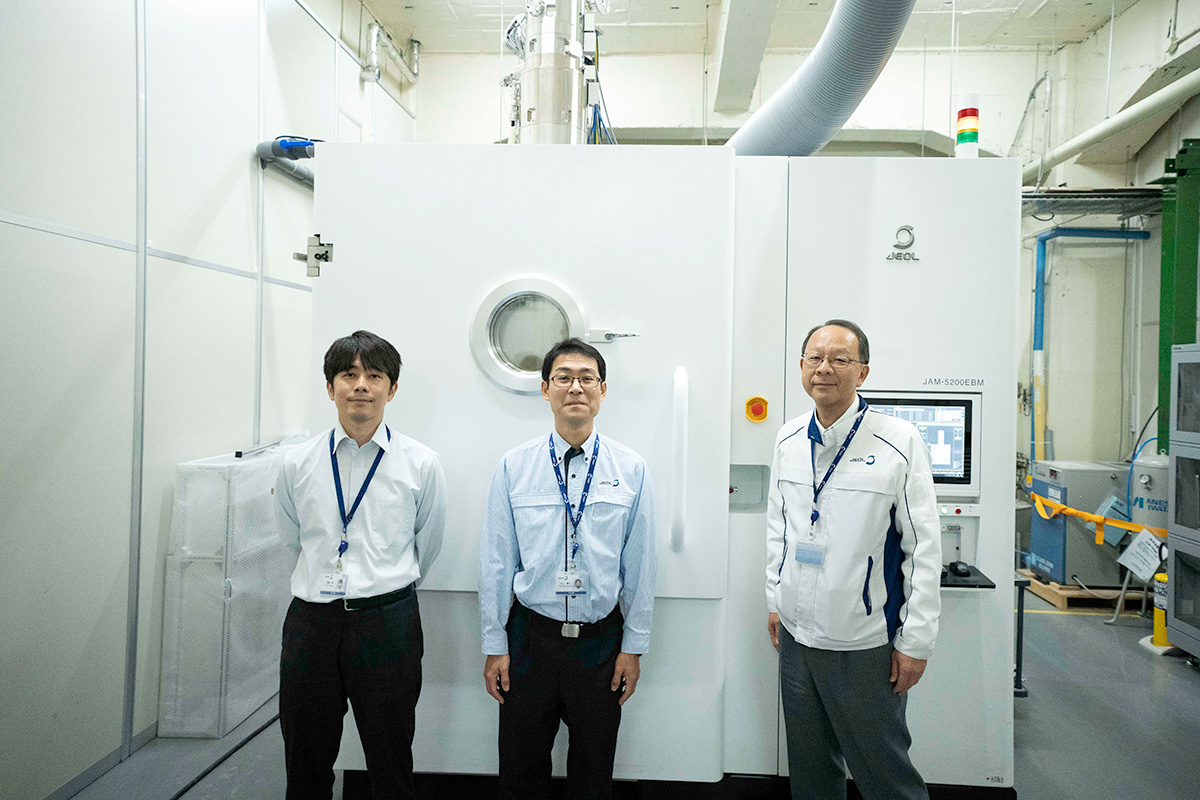
JEOL Ltd. is seeking to open up the future of manufacturing by challenging a new field of metal 3D printers. At the center of these efforts is the "JAM-5200EBM" which utilizes our electron beam technologies. This instrument enables processing metals of high-melting point such as tungsten, and is expected to be used in sophisticated industries such as aerospace and medical. This report introduces the development background, difficulties, and the hope and future prospects of the product by interviewing the member of the development team including the project leader of Hironobu Manabe.
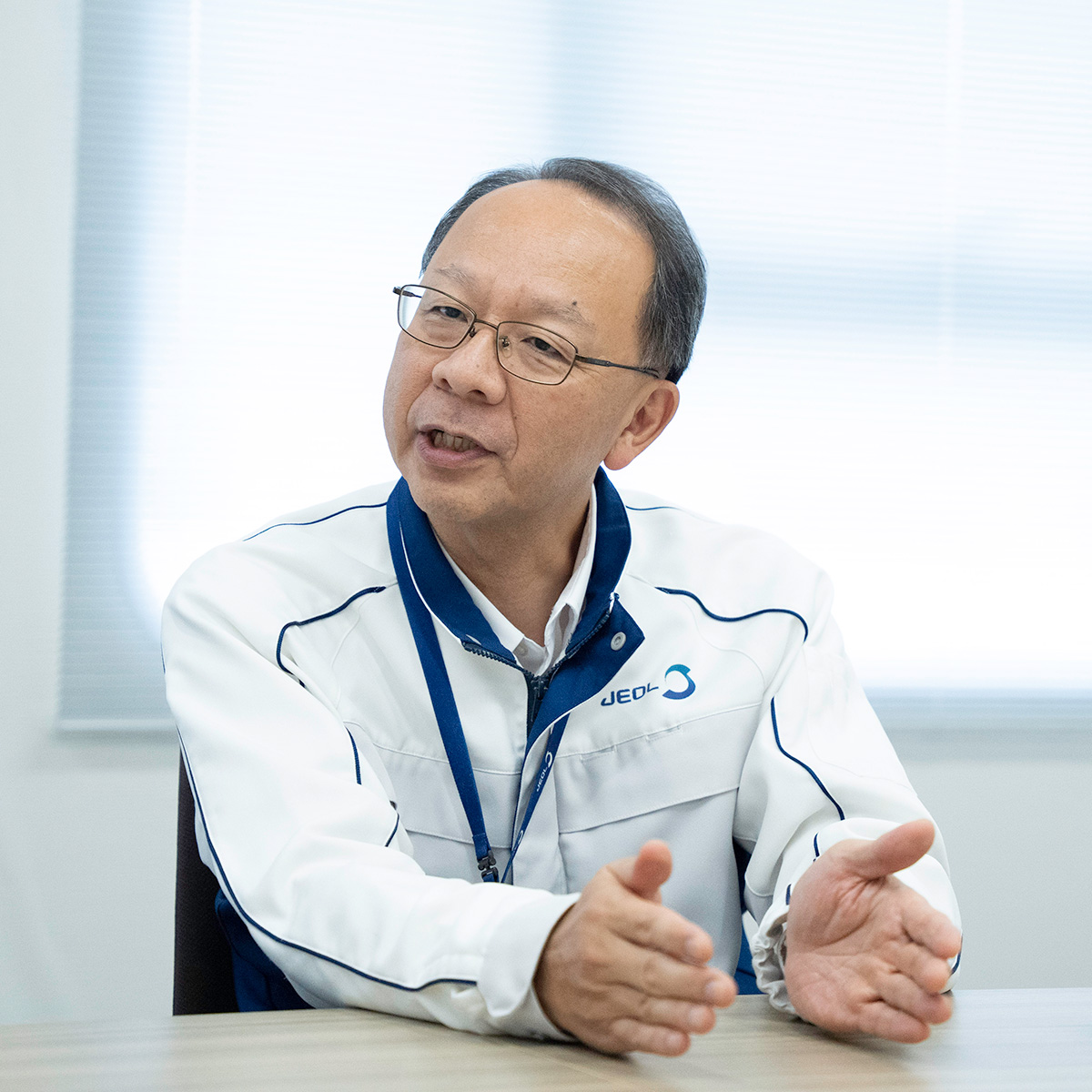
General Manager
3D Additive Manufacturing Project
Hironobu MANABE
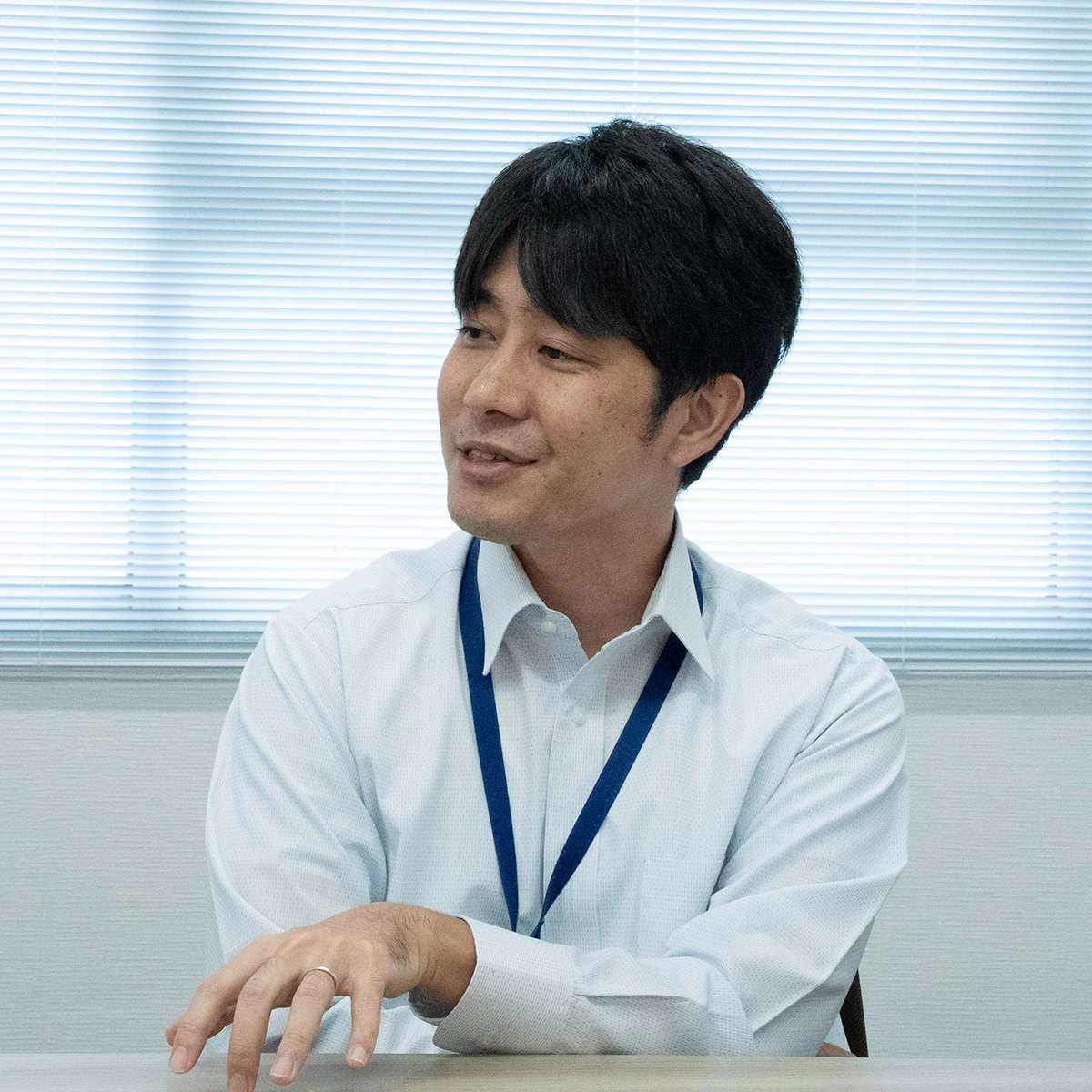
Assistant General Manager
3D Additive Manufacturing Project
Takashi SATO
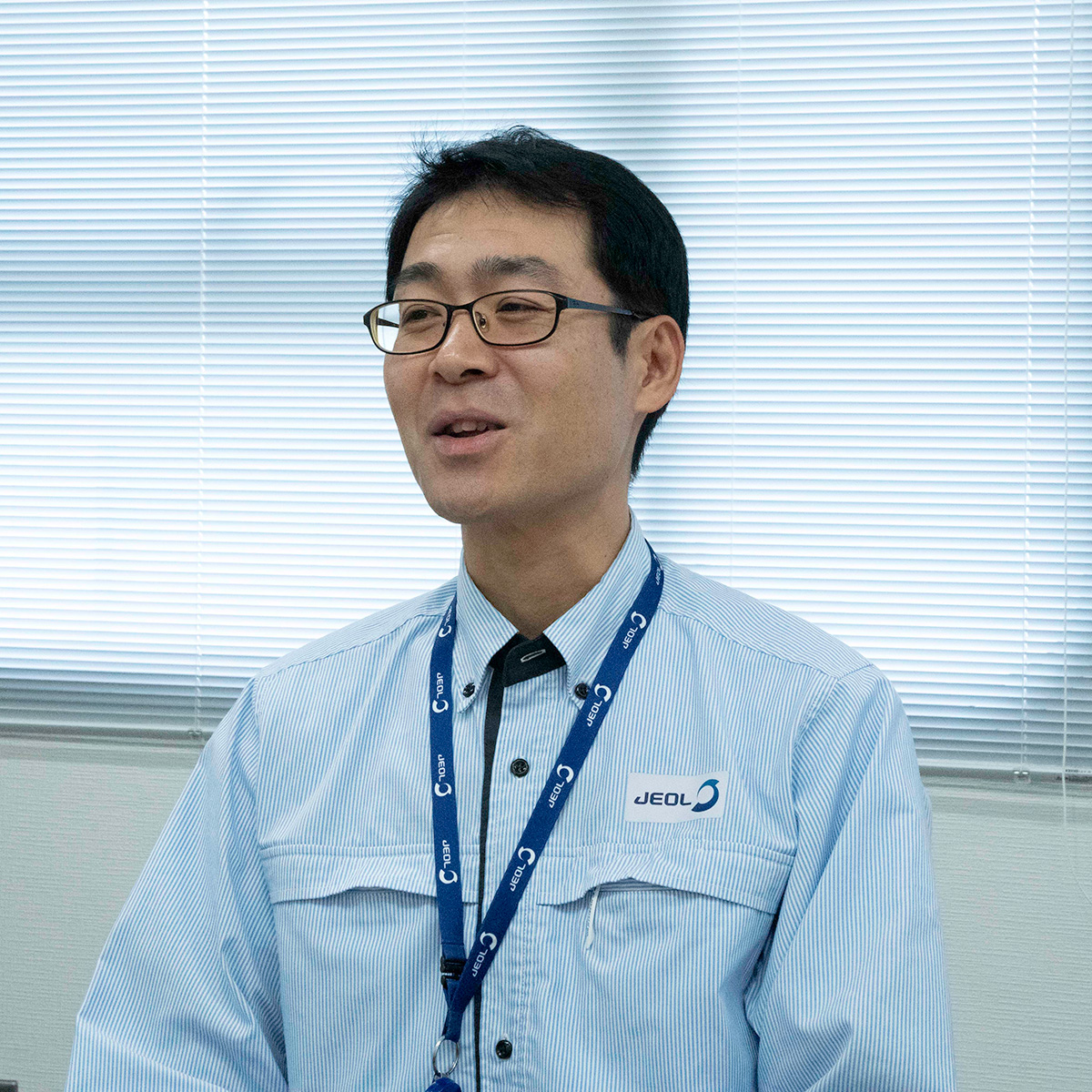
Assistant Manager
3D Additive Manufacturing Project Design Group
Nobuhisa YAMAGAMI
Feeling a sense of crisis: Japan is falling behind the rest of the world
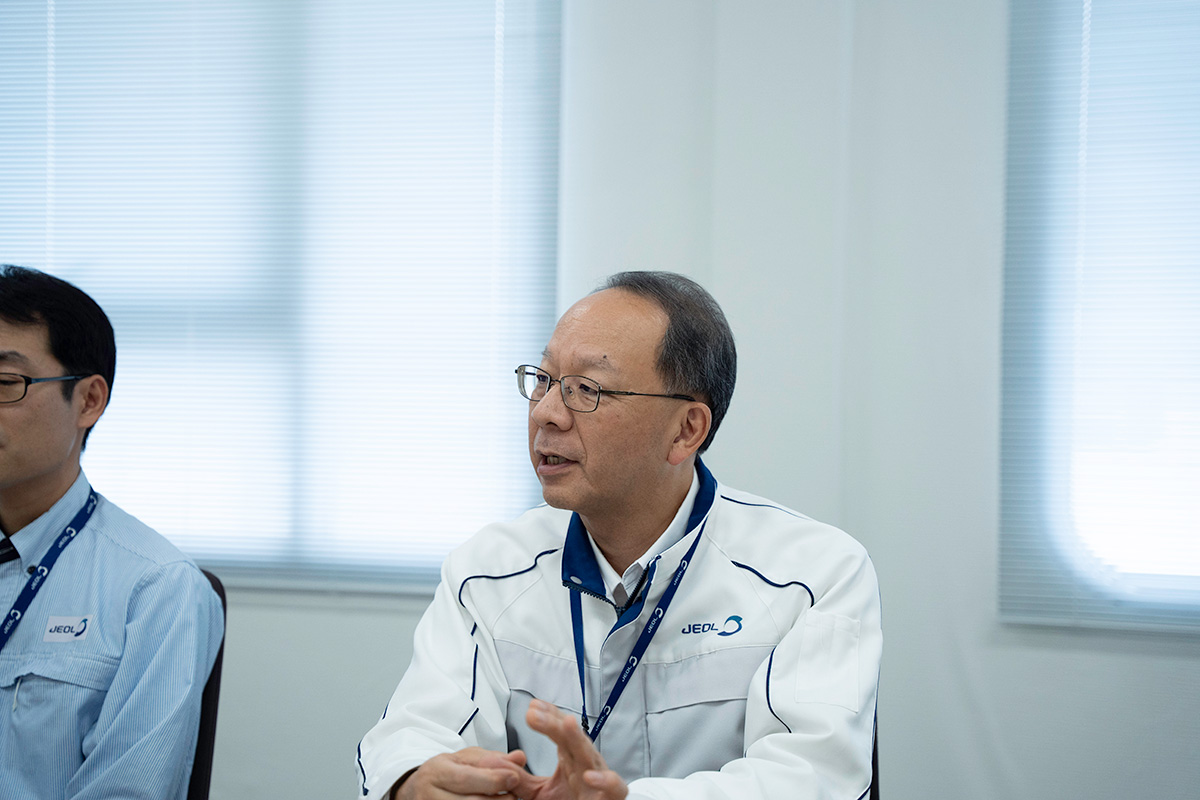
―― Why did JEOL come to develop a metal 3D printer?
Manabe: The trigger was the project called "TRAFAM" led by the ministry of economy, trade, and industry in 2014. At that time, Japan was greatly behind the U.S.A. and Europe in the field of metal 3D printer. Above all, in aviation and aerospace industries, manufacturing of light-weighed or complex structure building by using 3D printer was ongoing. I felt the sense of crisis against the situation where Japan is losing its competitiveness in this field.
―― Why was JEOL selected?
Manabe: JEOL had global record in electron beam technology field. Also, some researchers such as Prof. Chiba, of Tohoku University highly evaluated JEOL that "JEOL is the only company that can utilize electron beam technology in metal processing". It was also the key factor. As a country, I think there were high expectations for JEOL as a member of Japan's manufacturing industry.
―― What kind of opinions did you have in promoting this project internally?
Manabe: 3D printers are not the mainstream business in our company. Some say "is it really possible?". However, I found a new possibility to utilize our electron beam technologies in this field and explain it to the management people. The condition was severe, which is to complete prototype in one year. However, I believed in the ability of engineers in JEOL and pushed the project forward.
Engaged in the development by leveraging past experience in other departments
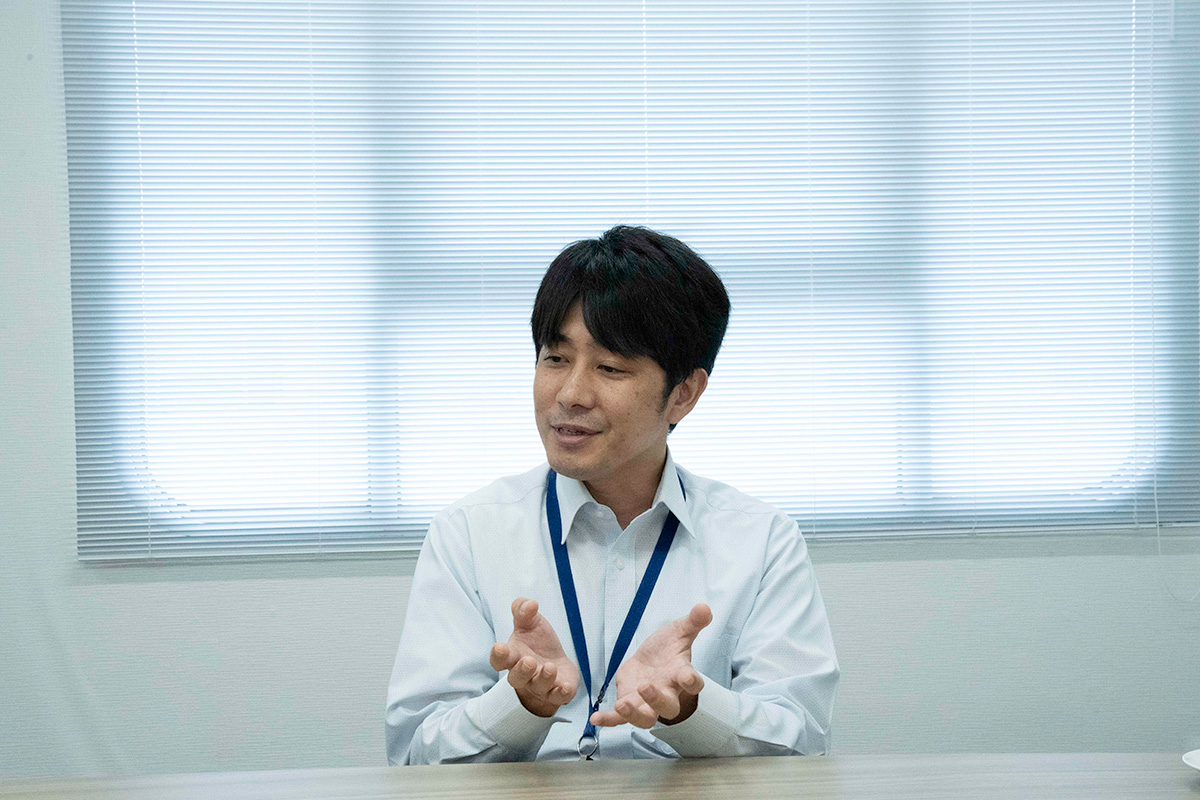
―― What was your role in the project?
Sato: I have managed the project from the product design to mass-production as group leader of technical group. To be concrete, I have determined the process from prototyping stage to practical use with the design team and worked on improving the prototype and production efficiency.
After entered JEOL, I have been working on developing electron gun in semiconductor field. The know-how I have developed helped us a lot in this project. In addition, during development unexpected issues have occurred. I played the role to judge the essence of the issue and make resolution quickly, as the designer.
Yamagami: I was in charge of electric design in the design group. Especially, I worked on designing to secure safety of the entire instrument and acquisition of authentication to cope with the strict safety regulations that is required in the overseas market. Before then, I was in charge of electric design of analyzers, and I think I could make use of the knowledge of signal processing and circuit design in this project.
In addition, in large instrument such as the JAM-5200EBM, all parts need to operate
together.
Therefore, I have thoroughly revied the design for stabilized control system and preventing
malfunction, ultimately resulting in an instrument that is both durable and reliable.
Manabe: I was in the position of managing the entire project. My role was not only to determine the direction of development, but also to control the progress as the governmental project and to boost morale of the team. In my career, I used to work on the instrument that is highly reputed both in Japan and overseas, such as ion beam system and electron beam lithography system. Through the experiences, I have developed the capability to see through technical issues and the point of view to overview the entire project. Strict conditions had been given as it was a governmental project. By promoting the project while believing in the technical expertise and tenacity of all the members, we successfully achieved our goal.
Struggled with securing stability and acquiring authentication of the instrument
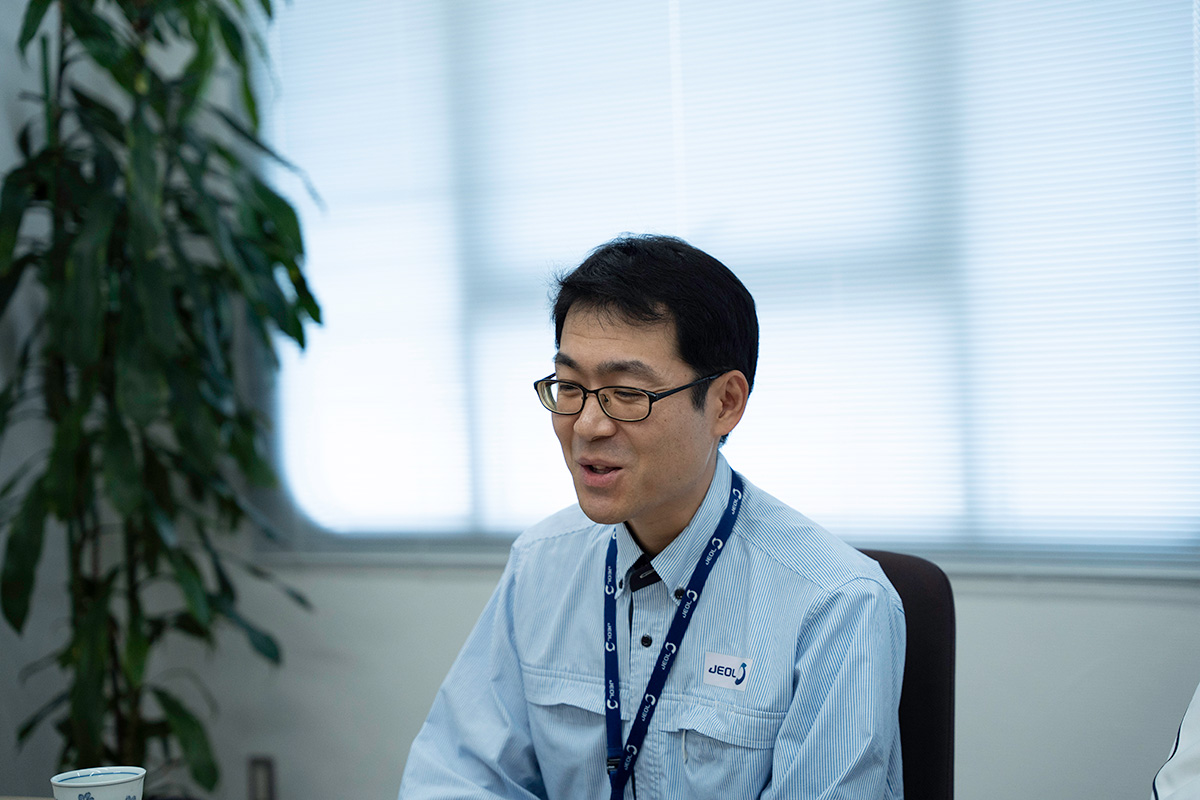
―― What was the issue that you have faced during developing the JAM-5200EBM?
Sato: Ensuring equipment stability was a major challenge. We had to make many corrections during the prototype stage due to problems such as the electron beam stopping halfway through the process and the powder not being evenly spread, etc. Since it can take several days to manufacture a single part, we could not have a person watching over the part the entire time. However, if we went to check on a part and found that it had stopped in the middle of production, we would not be able to put it into practical use.
In order to realize unattended operation while human is not attended, we made improvement of hardware and software repeatedly.
Yamagami: Acquisition of overseas safety regulations and quality authentication is the difficulty I had. In particular, aviation and space fields requires extremely strict standards and it was tough to conduct designing to cope with them. I had hard time to balance securing safety and reducing instrument costs.
Manabe: As I mentioned earlier, the condition of completing the prototype in the first fiscal year was extremely difficult. However, I have never felt that "production may not be possible". This is because I believed in the members. As a result, we were able to complete the prototype within the limited time and budget due to the efforts of each engineer.
Advantages in processing metals of high melting-point
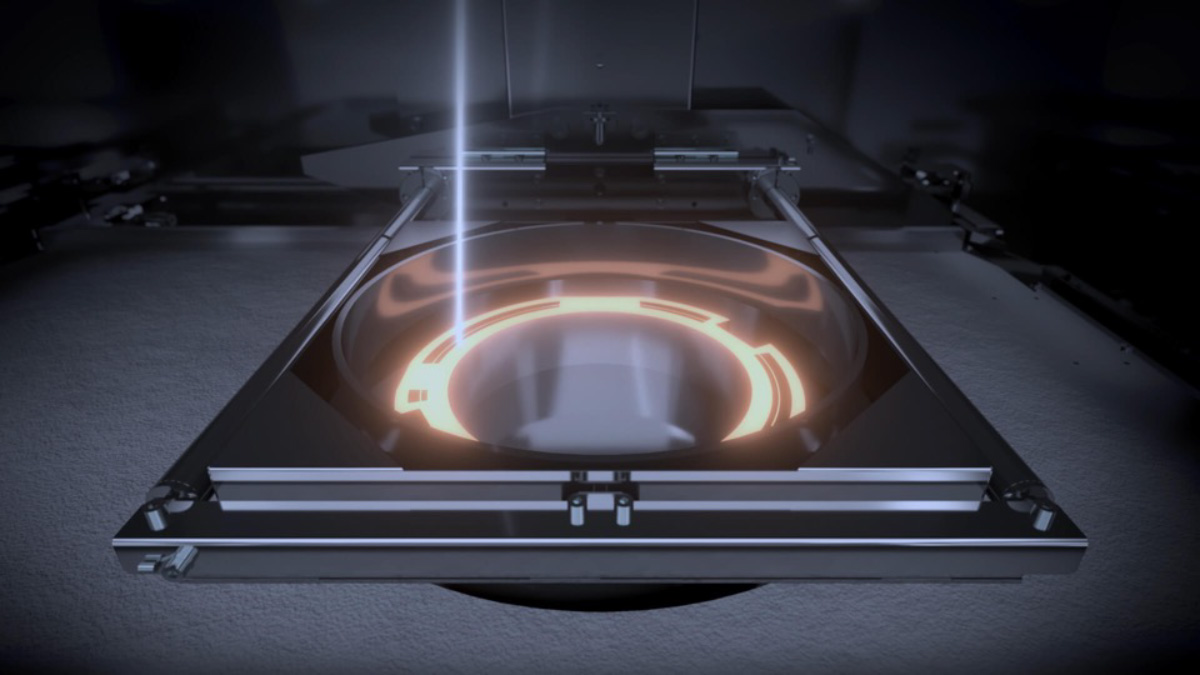
―― What is the feature of the JAM-5200EBM, compared with products of our competitors?
Sato: The most outstanding feature of the JAM-5200EBM is its ability to processing high melting point metals such as tungsten and molybdenum while preheating the workpiece at a high temperature of 1,600°C.These metals that are difficult to handle by products of our competitors, can be safely modeled with our electron beam technologies.
Yamagami: In addition, acquisition of AMS authentication is another. This has realized the strict quality standard of aviation and space industries. Also, the instrument provides excellent reliability and durability.
Manabe: The JAM-5200EBM not only model metals, but also create an inner structure that cannot be achieved with conventional cutting. While cutting cannot create a hollow inner structure, a 3D printer can. It leads to weight reduction of parts and reduction of raw material contributes to cost reduction. I think that the high degree of freedom is the greatest appeal of 3D printer technologies.
Cherish inspiration and never give up till the end
Sato: I deeply sympathize with Thomas Edison's statement,"Genius is one
percent inspiration and ninety-nine percent perspiration".
This phrase does not to simply mean that
"efforts alone is not enough", but to indicate that the initial direction is quite important for a success"
I think. For example, I had many scenes where I strongly felt how serious the goal of the specification and
design that are set at the early stages of development can give significant impact to the outcome
ultimately. For this reason, I have always made a constant effort to find that "1% inspiration" through
discussions with my team.
Yamagami: My belief is the attitude to "challenge without fear of failure". At the technical development sites, it is important not to give up after failures once or twice, but to learn what to learn from the failures. During developing the JAM-5200EBM, I also faced troubles many times at the prototyping stage. In such a situation, I kept my belief "to challenge without fear of failure". This way of thinking was utilized in my research in plasma physics field while I was a university student. I cultivated the attitude not only to follow the theory but also to approach the essence while repeating experiments.
Manabe: I was greatly influenced by the teachings of Eiichi Shibusawa and Kazuo Inamori. Especially, the words of Mr. Inamura that "never give up until the end" is something I always kept in my mind while I promoted the project. For example, we need to overcome many issues with the budget and timeframe limited as the project with the government aid needs quite strict status control. While I kept thinking about how to overcome the difficulties with the team, I truly felt the importance of the words. Also, the words of Eiichi Shibusawa of "the importance of being sincere" is another belief of mine. As an engineer, I feels it inevitable to be sincere, in order to provide customers with reliable products.
I would like to devote myself to improving Japan's competitiveness and nurturing future generations.
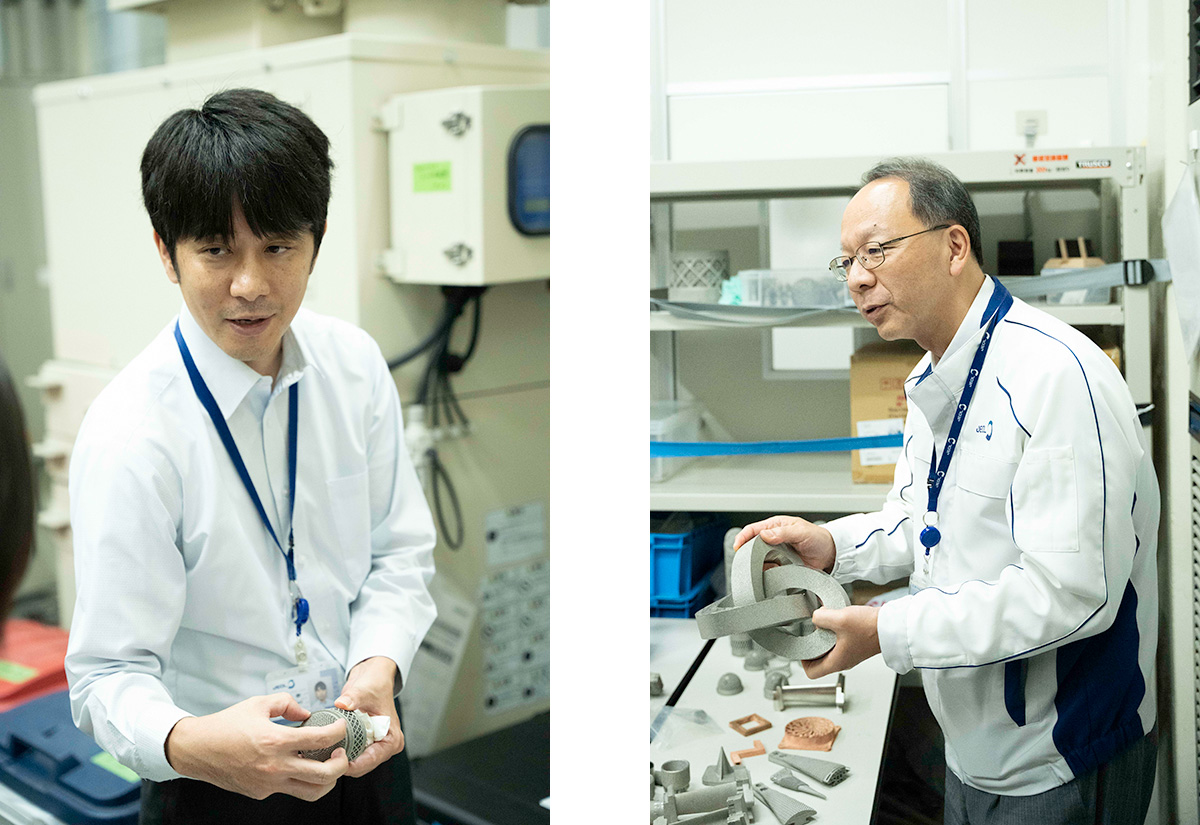
―― Lastly, please tell us about what you would like to achieve in the future and your enthusiasm for it.
Manabe: Now I am away from the project and I believe that the technology of the JAM-5200EBM will improve the competitiveness of Japan in metal 3D printer field. We need to continue developing more efficient and multi-functional instrument, based on the know-how obtained through the attempts in the past. Also, we should not only manufacture instruments, but also focus on after-sales support and technical training, so that customer can optimized the value of the instrument.
This instrument is expected to be used in advanced industries such as aviation/space, and medicine. I expect it will be applied in even more diverse fields in the future.
Sato: My role is to pass the experience and technologies that I have cultivated at site to younger people and support the development of the next generation model. In particular, the knowledge we obtained through mass production and practical use of the JAM-5200EBM, must be definitely useful when younger people develop new product. Also, we need to pursue cost reduction and productivity improvement in the next generation model further. For example, by applying instruments that used to be designated for special metals such as tungsten and molybdenum, for materials of higher versatility, there is a possibility to expand the entire metal 3D printer market, I think.
Yamagami: Realizing safety and efficiency is the great issue in developing the next generation model. In developing the JAM-5200EBM, we repeated designing and testing to cope with the strict standards of aviation/space industries. By utilizing the experience, we are aiming for an instrument that can be utilized in more versatile industries. In addition, I want to reinforce the user-friendly design and establish a system that allows for easy operation to companies who use 3D printers for the first time. I would like to contribute to improve competitiveness in the entire industries in Japan, by aggressively working on the regulation authentication in Japan and overseas and improving energy efficiency.