Continuous feeding of 10 μ or less fine powder
Features
Continuous quantitative feed of under a few micron particles with highly cohesive and poor fluidity.※
Powder feeding rate is around 0.1 to 100 g/min or more by changing option items.※
Because of the closed structure, it is possible to feed into reduced-pressure atmosphere. (e.g. 100 Pa)
Can monitor and record the real-time powder feeding rate and the total feed amount. (Option)
Not only single powder but also mixed powder can be fed continuously without changing mixing ratio.
The feeding condition differs according to the powder type, size, shape, weight and state.
Feed principle(Image figure)
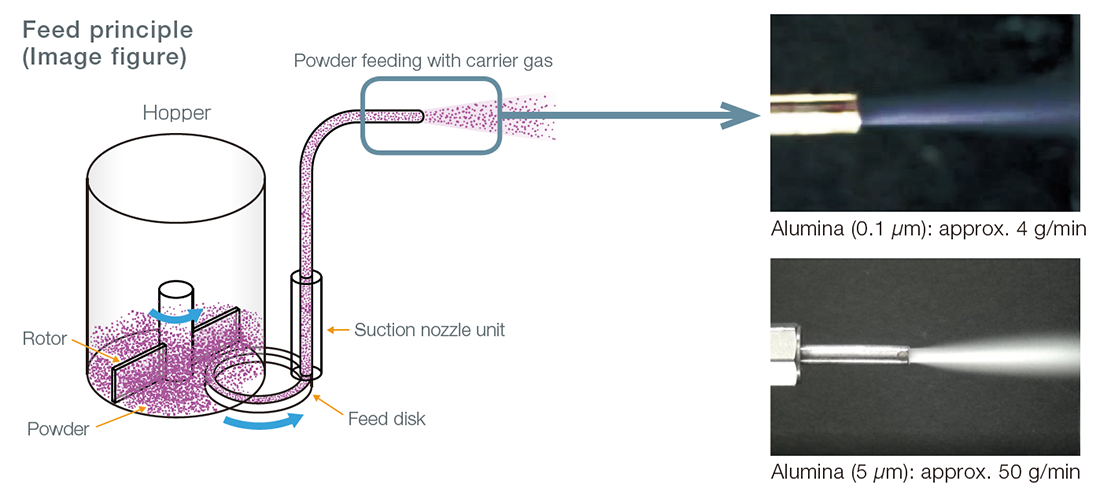
Applications
Thermal Spray(Plasma Spray)/Aerosol Deposition/
Additive Manufacturing(3D Printing)
Specifications
Specifications
Powder particle size | Approx. 0.1 to 100 μm or more ※1 |
---|---|
Powder feed rate | Approx. 0.1 to 100 g/min or more ※2 |
Feed method | Table type, gas carrier |
Adaptive gas type | Ar, N2, Air |
Gas flow control system | Not included |
Gas purity | 99.9% or more |
Gas pressure | Max. 0.6 MPa / Normal use 0.3 MPa or less ※3 |
Gas flow rate | 1 to 20 L/min or more ※4 |
Vacuum resistance | Leak degree: approx. +2 kPa (or less) in 10 minutes ※5 |
Hopper capacity | Approx. 500 mL ※6 |
Size / Mass (Powder feeder) | Approx. 280 mm (W) × 211 mm (D) × 541 mm (H) / Approx. 21 kg |
Size / Mass (Controller) | Approx. 211 mm (W) × 280 mm (D) × 211 mm (H) / Approx. 5 kg |
Input power / Grounding | Single-phase 100 to 120 V (-15 to +10%) 50/60 Hz 10 A / 100 Ω or less (1 terminal each for the feeder and the controller) |
The range of powder particle size that can be fed differs depending on the type, shape and state of the powder.
We have experienced 200 to 300 μm powder.The feeding rate range differs depending on the powder type, particle size, shape, state, optional item configuration and carrier gas conditions.
We recommend the use of Mass Flow Controller, because the gas pressure needs to be constant for stable feeding.
Depending on the tube diameter and length, 20 L/min may not be supplied. If the gas flow is too low, powder may not be fed.
It changes with the consumption degree of O-ring. O-rings need to be replaced regularly.
The capacity can be increased by mounting an optional hopper.
Required optional items
Suction Nozzle Unit | Pipe diameter: 1 mm type / 2 mm type / 3 mm type |
---|---|
Feed Disk | Groove width: 1 mm type / 3 mm type / 5 mm type / 10 mm type |
Options
Power Feed Rate Monitor Set | Measure powder feed rate in real time. 1) Electronic balance 2) PC 3) Communication cable 4) Software |
---|---|
Convex Flange Unit | Loosen highly cohesive powder that has solidified in the groove of the Feed Disk. |
Gearbox | The ratio of Feed Disk:Rotor can be changed to 1:2 and 1:3. (Standard: 1:4) |
Additional Hopper | 1 L (Total approx. 1.5 L) *Consult us for other additional hopper. |
Internal Observation Window | Can visually observe the remaining state of the powder in the hopper. |
Catalogue Download
TP-99140FDR Fine Powder Feeder
More Info


Are you a medical professional or personnel engaged in medical care?
No
Please be reminded that these pages are not intended to provide the general public with information about the products.