NDK Inc.
~Metal 3D Printer supporting advancement of induction hardening technology
NDK Inc. has a long proven history in the field of induction hardening technology and is aiming for further advancement by adopting metal additive manufacturing technology.
In this interview, we asked NDK in detail about how NDK introduced the metal 3D printer, its future perspective, and its expectations for JEOL Ltd.
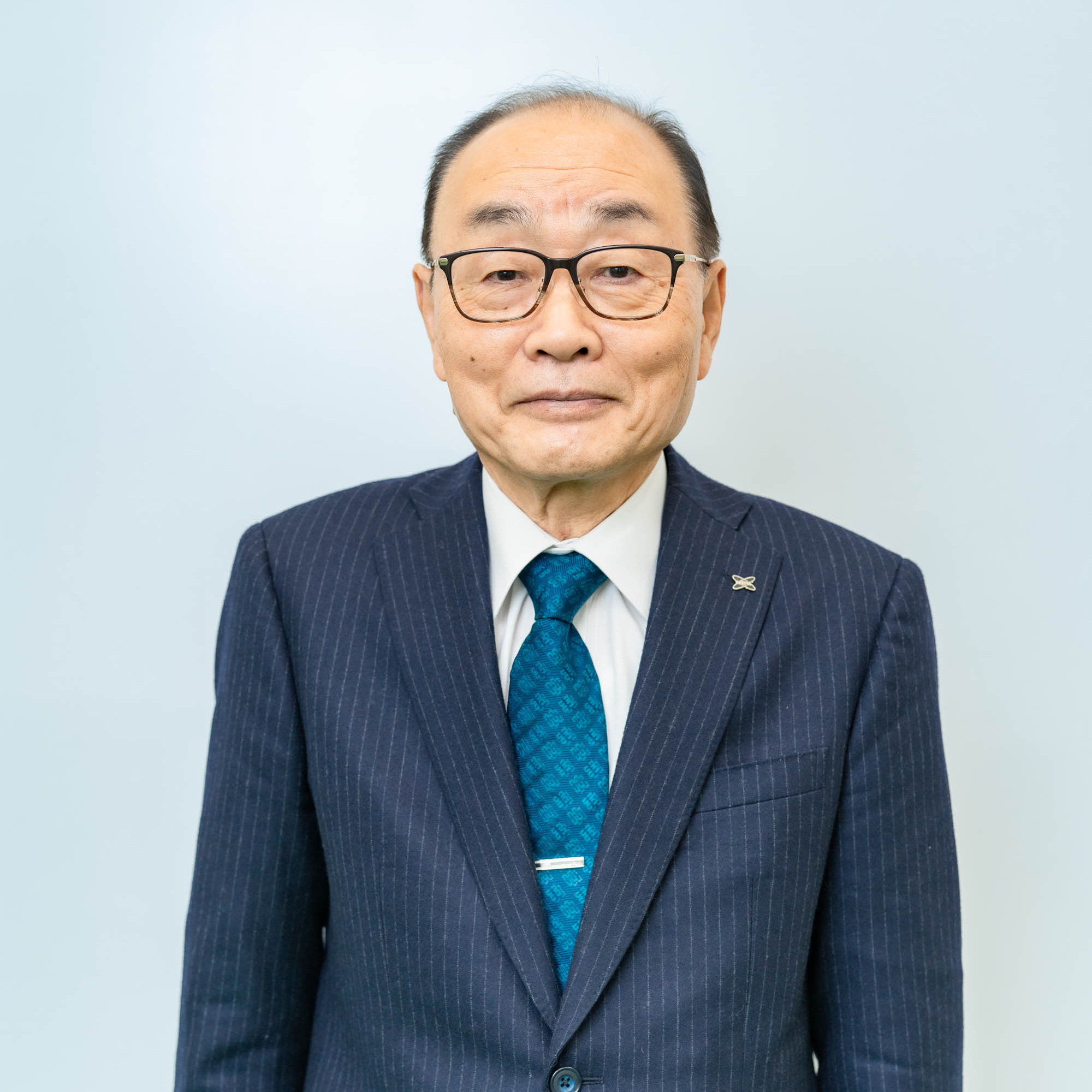
Hirotsugu Takeuchi
President, NDK Inc.
After graduation from the Department of Metallurgical Engineering, Faculty of Engineering, Kansai University, he joined NDK Inc. in 1977. He was in charge of technical development in the equipment manufacturing department and engaged in developing plasma (ion) nitriding technology. Later, to enhance his expertise, he entered the doctoral program in material science at the Graduate School of Science and Engineering, Ibaraki University and earned a doctorate in engineering. While in graduate school, he managed both work and academic pursuits while receiving guidance from a professor of Ibaraki Univ. At the age of 49, he was appointed as a director and served as president of a subsidiary for the next 11 years. At the age of 58, he was appointed as president of NDK Inc. and has remained in this position to the present.
Introduced Metal 3D Printer JAM-5200EBM to realize in-house production
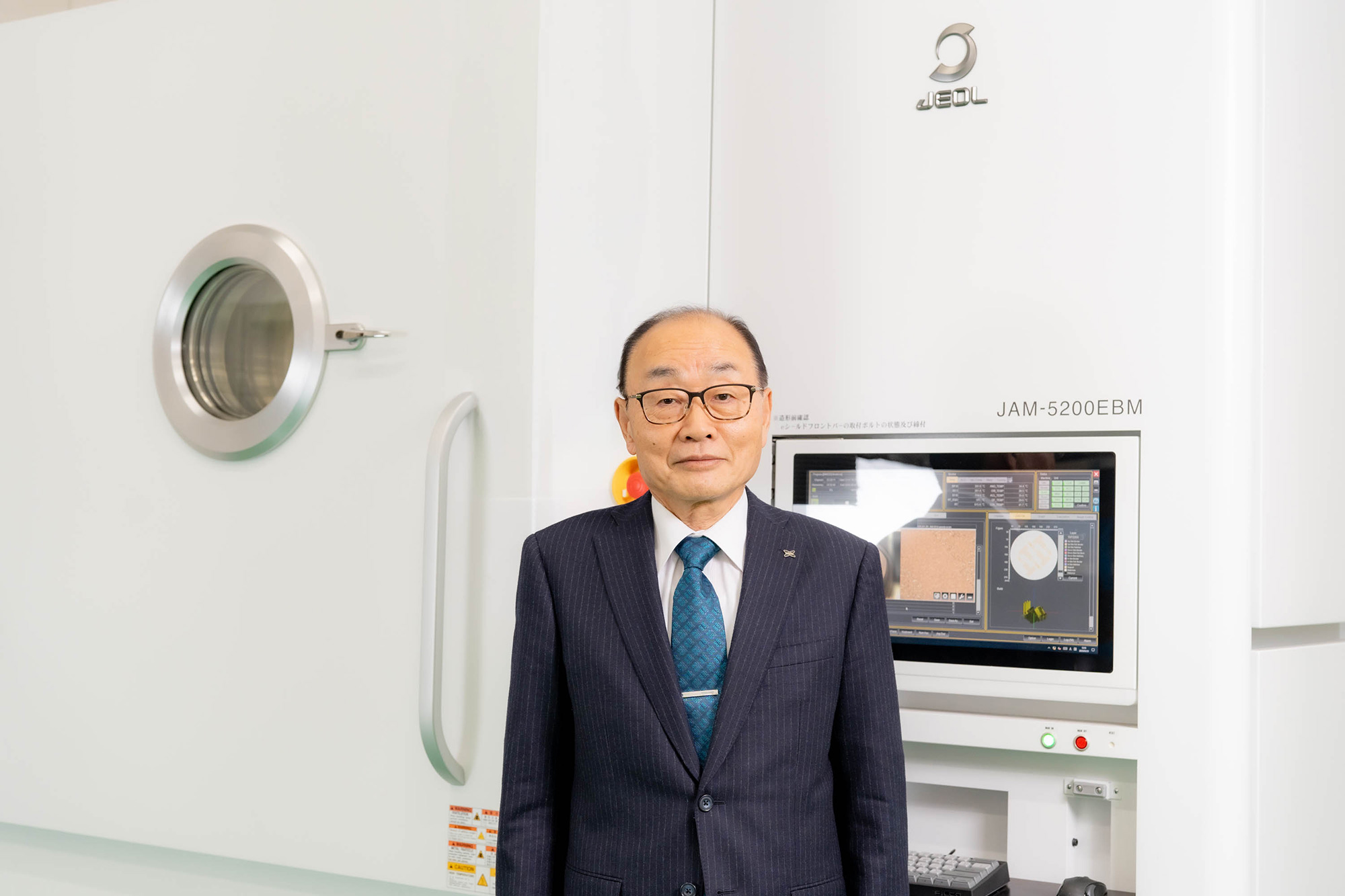
―― Would you tell us how your company introduced the metal 3D printer?
Our company has been dealing with contract processing of induction hardening for steel materials and manufacturing and marketing of the equipment for many years. Heating coils made of copper are inevitable for induction hardening. We used to use the coils prepared by our associate companies by cutting, bending, hole making, and brazing. However, there were times when they did not satisfy certain requirements. In addition, we thought that it would be necessary to produce the heating coils in-house rather than asking an associate company to produce them. This would help us obtain contract processing orders steadily in the future, as the heating coils are essential parts for induction hardening.
With such a background, we started to consider introducing metal 3D printers. Realization of complex-shaped coils using a metal 3D printer and a stable supply from in-house production were thought to improve customer satisfaction and expand our orders. Also, by offering the coils as an attachment when our instruments are sold, we could expect stable orders.
―― For what reason, did you choose the electron beam type metal 3D printer?
Our copper heating coils are not made of copper alloy, but of pure copper. Cost-wise, pure copper is more expensive. Nonetheless, we decided that use of pure copper would be better when calculating the whole power costs because pure copper has high electrical conductivity.
There are two types of metal 3D printers: electron beam type and laser type. We have chosen the electron beam type, as the electron beam type of high energy conversion efficiency is better for modeling pure copper. For modeling copper alloy, a laser type would do, but for pure copper, we thought that the electron beam type would be better.
―― Why did you choose JEOL over other manufacturers?
Some Japanese manufacturers provide metal 3D printers of the laser type, but only JEOL provides the electron beam type.
Also, we have a long historical relationship with JEOL and JEOL is an important stockholder as well. Another point for our selection of JEOL is that we have tremendous confidence in JEOL as the top manufacturer in the world who produces sophisticated analytical instruments such as electron microscopes as well as industrial equipment.
―― How has the introduction changed your company's manufacturing process?
Although no major changes have been made yet, we are aiming for improved quality of the heating coil and shorter manufacturing time before delivery. We are highly rated by our customers, because the prototyping that took a couple of weeks for an associate company can now be ready in a couple of days due to in-house production.
Ease of use of the equipment is extremely high. We feel that it was designed from the user's perspective. On the other hand, there is room for improvement in removing copper powders and in the cooling process of highly heated copper. We are hoping to seek further improvements in efficiency.
Further advancement is expected such as AI adoption in the future
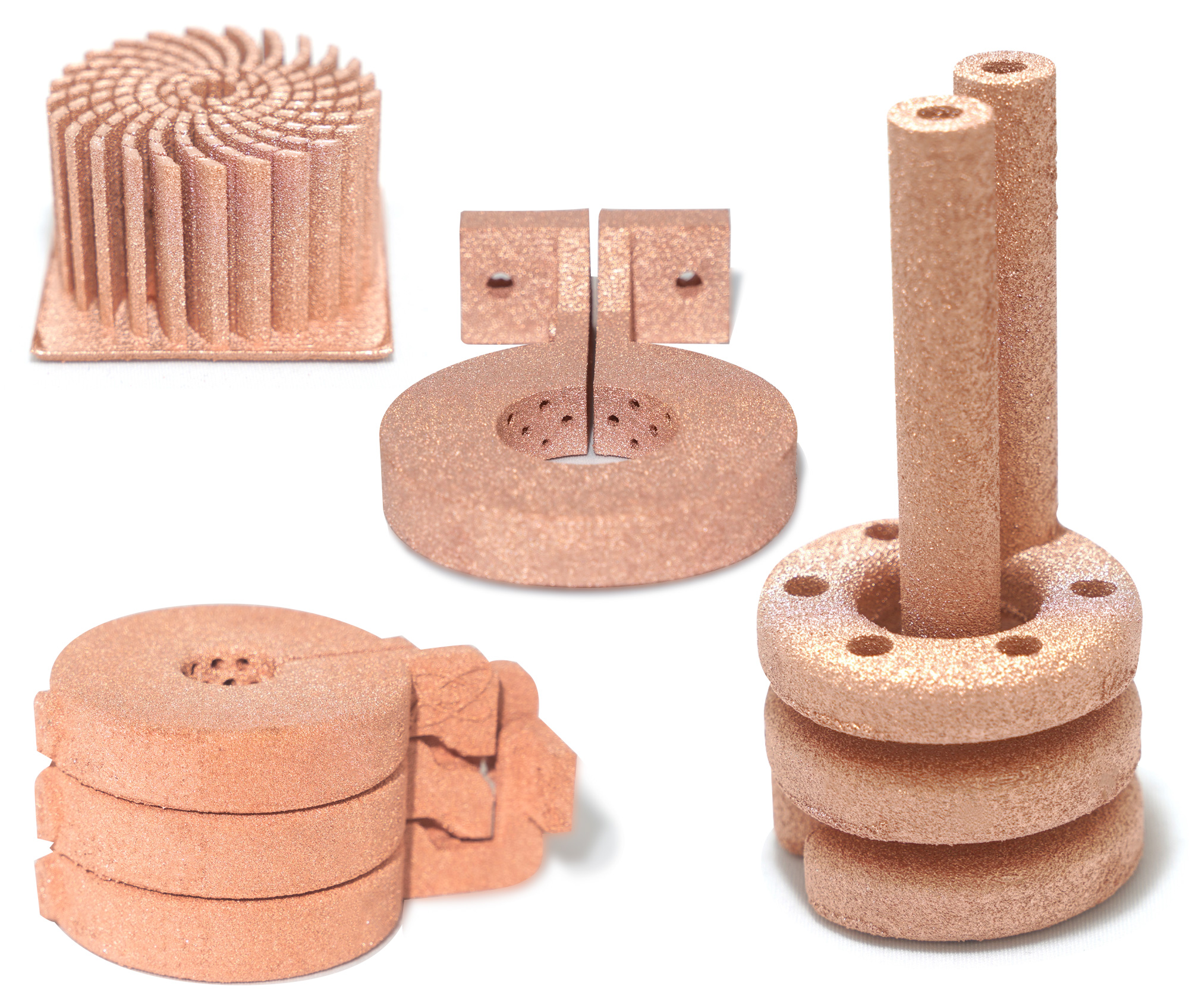
―― What results have you seen in terms of cost reduction and improved productivity since the introduction of the system?
As it is not long before the operation start, we use the 3D printer mainly in manufacturing prototypes. Cost reduction and improved productivity will be the challenges in the future. But we are talking with JEOL's representative to reduce the cost of copper powder disposal.
―― Is there any plans for new business by utilizing "JAM-5200EBM"?
At present, it is used in manufacturing heating coils in-house mainly. However, we have inquiries for various prototypes including valves, electrical parts, and iron material for hardening processing. Above all, we are focusing on the development of parts that utilize electrical conductivity and thermal conductivity of copper. We would like to bring about new business by using these.
―― Is there any other points that you expect from JEOL's product?
Our company's core business is surface modification technologies such as induction hardening and ion nitriding of steel materials, PVD, and DLC coating. On the other hand, we are still inexperienced in additive manufacturing technology, so we would like to advance our business under the guidance of JEOL.
In addition, "AI" has been a widely discussed topic in recent years, and we would like to see it incorporated into industrial machinery. For example, it would be easier to use if there were a function that could automatically manufacture products by inputting data and setting conditions.
Issues with smoothness of mold surface
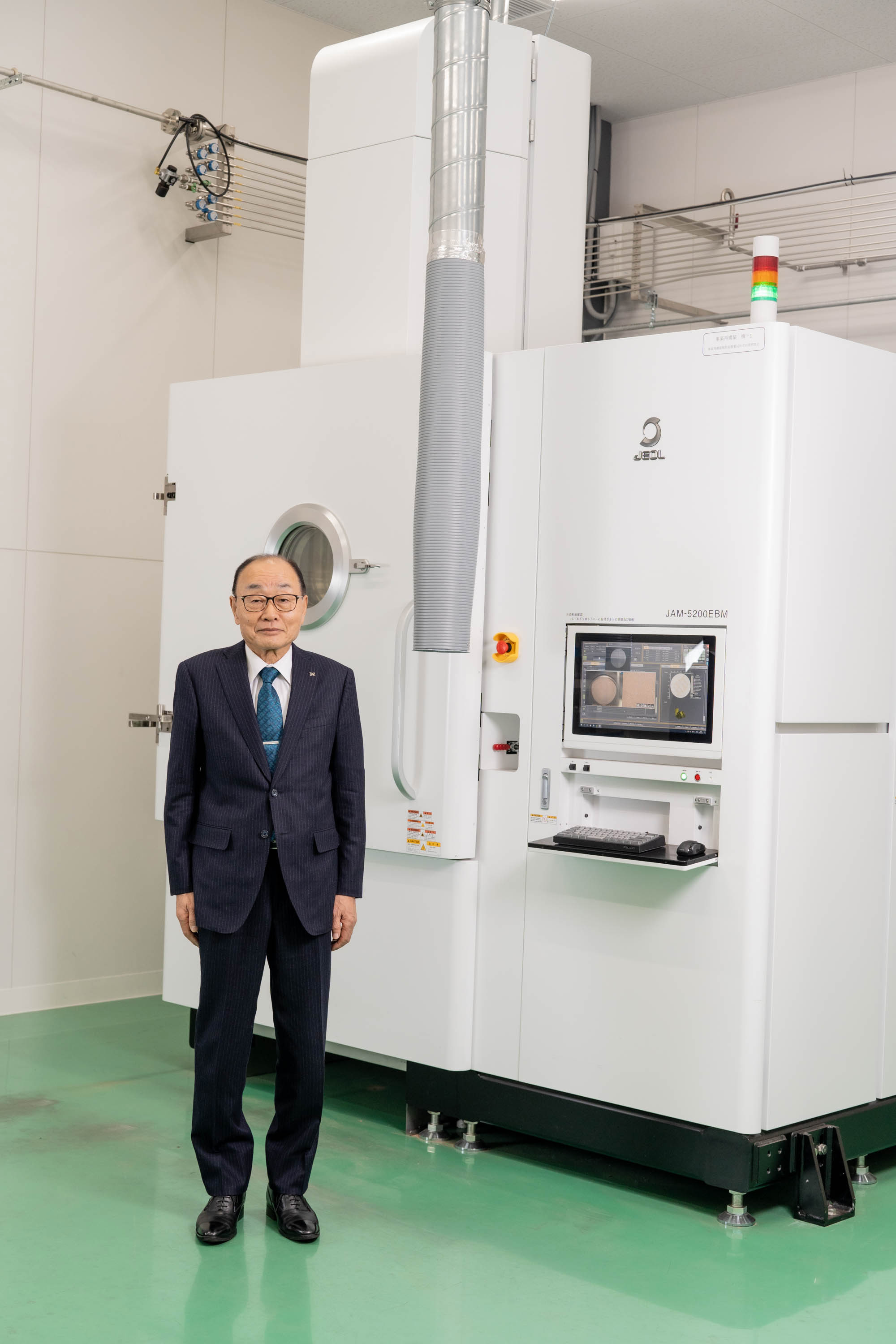
―― Please tell us about any difficulties or challenges you faced in introducing the system.
The issues are removal of metal powder remaining inside the molded product and improvement of surface roughness. Although there are no functional problems even in the current state, we believe that a smoother surface finish will enhance the product's value.
―― How would you evaluate the ease of operation and maintenance at the site?
It is quite easy to operate and maintain. We feel that the equipment is easy to use and places little burden on on-site workers.
―― What is your impression of the troubleshooting and support system after installation?
We have had prompt responses when we had some troubles. The coordination between sales, engineering, and services is excellent. The fulfilling support system gives us a great sense of security. For example, when dealing with foreign companies, they tend to be clear in their answers and clearly indicate "what they can and cannot do" in general. On the other hand, when we contacted JEOL's representative, people in sales, engineering, and services were all working together to support us. Therefore, we could use the equipment with peace of mind.
―― Are there any good points or areas that you feel need improvement, based on the feedback from the site?
Since it has only been in operation for a short period of time, there are still some issues to be addressed in terms of on-site proficiency. We intend to share with JEOL any points that we notice as the operation progresses and make improvements.
―― What kind of companies or organizations do you think this product would be suitable for, after actually utilizing this product?
This is the first attempt for us and it is a difficult question to answer. I think that it may be suitable for a development department at manufacturing industries such as automobile parts and research in an industrial technology center. In addition, it is possible to utilize it in developing parts of aluminum, copper, and titanium, and manufacturing semiconductor related parts. It may be difficult for small and medium-sized businesses to introduce it directly. But introduction in governmental facilities such as industrial center will create opportunities for many small and medium-sized businesses to use it. At exhibitions, we receive inquiries from the field that was beyond our expectations. This made me feel that there would be a possibility for the metal 3D printer to be utilized in a wide range of industrial fields.
―― Do you have any future plans for further utilization of the "JAM-5200EBM" at sites?
Currently, we use it mainly for manufacturing coils for high frequency heating for in-house use. But in the future, we would like to promote it to our customers of the High Frequency Induction Hardening Equipment and to use it to develop new products of high added-value. In addition, we will strive to further improve our technical capabilities with the aim of developing our business in an all-round manner.