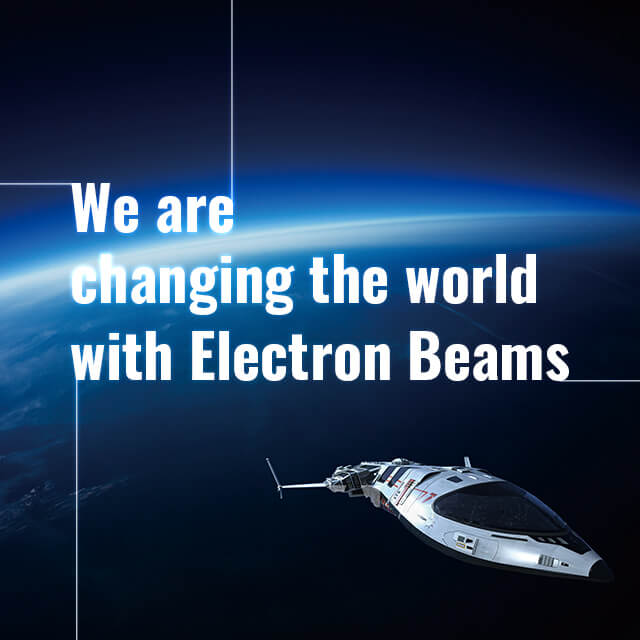
A little trip into space
Space travel, which was only a story in science fiction movies, is about to become a reality.
Yet, it is still not something that anyone can easily afford. One of the reasons space travel is so expensive is because of the cost of traveling by rocket.
JEOL's electron beam additive manufacturing technology has the potential
to drastically reduce the cost of rocket development, manufacturing, and even fuel.
The electron beam metal AM machine "JAM-5200EBM" makes it possible to reduce fuel consumption and increase output, reduce the cost, and shorten development time by high quality and high repeatability modeling, integration of multiple parts, and weight reduction.
Together with JEOL's additive manufacturing technology, innovation is advancing at an unprecedented speed.
Making “a little trip into space” a reality. We are changing the world with Electron Beams
JEOL Additive Manufacturing Technology
Using technology of the world's highest level performance electron microscope and electron beam lithography system for semiconductor manufacturing,
JEOL has developed an "Electron Beam Metal AM Machine" that can produce high-density, high-strength parts with high-power and high-speed electron beam.
It allows for cost savings and design freedom through increased productivity.
Long Life Cathode over 1,500 Hours and Helium-Free
for Smoke Prevention
Electron Beam Metal AM Machine
JAM-5200EBM
Main features
- High-power Beam (maximum 6kW)
- Long Life Cathode (1,500 hours or longer)
- Powder dispersal prevention system "e-Shield"
- Automatic Electron Beam Correction
- Heating Capacity: 1,100℃ or higher
- Remote Monitoring System
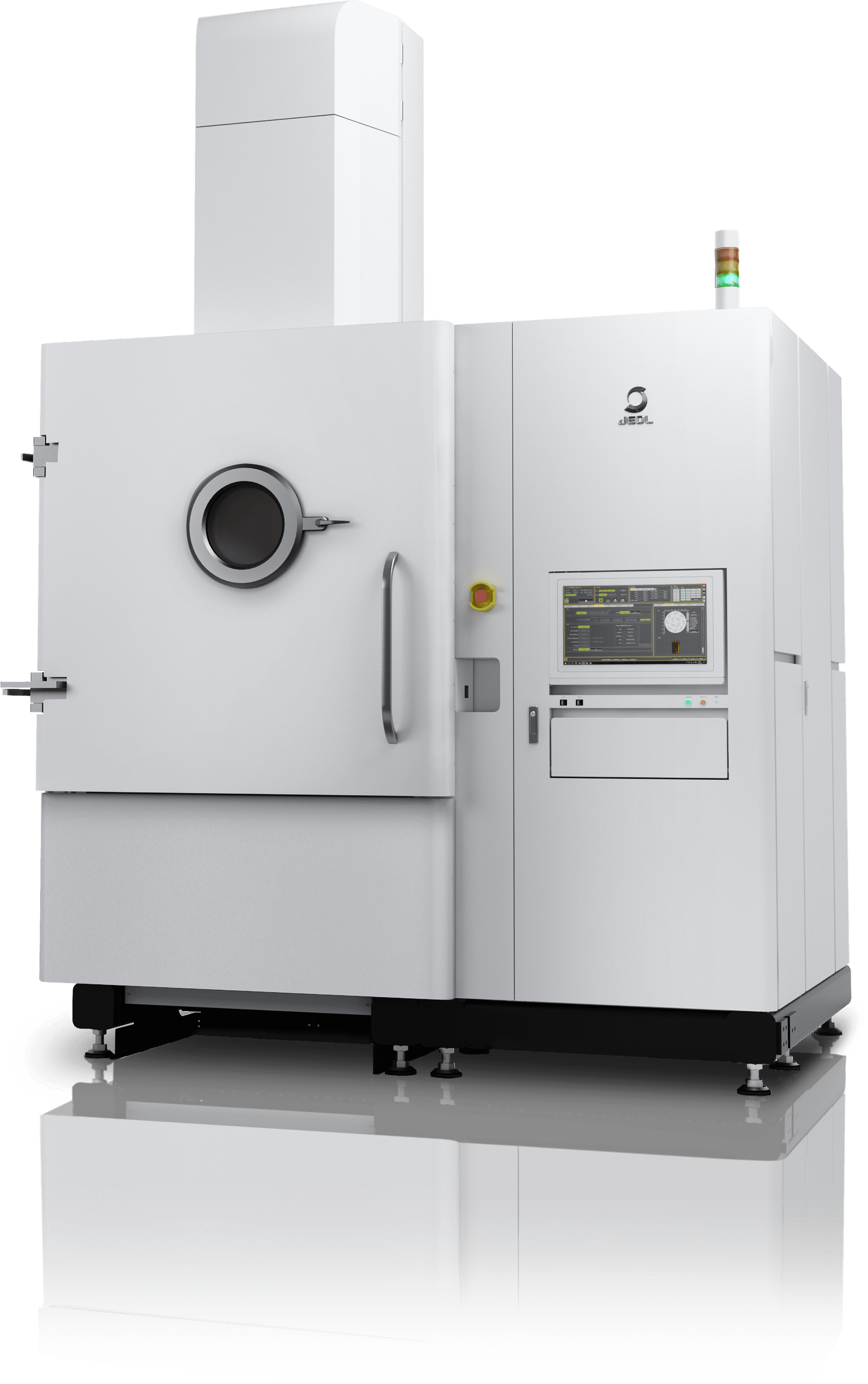
-
Long Life Cathode
"The Long Life Cathode, which lasts over 1,500 hours, can greatly reduce downtime for cathode replacement." The secret is JEOL's original vacuum technology, developed in the manufacturing of electron beam related equipment.
-
Helium-Free and powder dispersal prevention system
"e-Shield"No helium gas is needed to prevent scattering of powder. JEOL's unique powder dispersal prevention system, e-Shield and JEOL’s scan strategy avoid Smoke phenomenon. Thanks to the helium-free environment, not only can parts be manufactured in a clean space at a low-cost, but "the surface of the cathode is also less susceptible to damage, allowing the electron beam to remain stable." As a result, the manufacturing quality can be maintained until the end of the cathode’s lifetime.
-
Automatic Electron Beam Correction
The focus and spot shape of the electron beam are automatically corrected according to the irradiation position by the technology developed in our electron beam lithography system for semiconductor manufacturing.
This enables high-quality and highly reproducible manufacturing in the whole building area.
Image of beam correction
(right: Corrected (JAM-5200EBM)) -
Remote Monitoring System
The manufacturing status and the machine conditions can be checked from a remote location at any time. An alarm notification function is also available.
-
Realization of an eco-friendly and sustainable society
With JEOL’s “Electron Beam Metal AM Machine”, you can build more than one part in a single printing process. Almost no cutting is required, preventing materials from being wasted.
Reusing metal powder is another possibility. Thus, JEOL is working on the realization of an eco-friendly and sustainable society.
Technical Data
JAM-5200EBM
Main Specifications
Manufacturing method | Powder Bed Fusion |
---|---|
Process | Hot process |
Building dimensions | Maximum 250 mm (Dia.) × 400 mm (H) |
Electron beam output | Max. 6 kW |
Heating capability | Max. 1,100℃ or higher |
Cathode lifetime | 1,500 h or longer |
Powder dispersal prevention unit | e-Shield |
Inert gas (for smoke prevention) | Not required |
Chamber pressure (melting process) | 1×10-2 Pa or lower |
Electron beam correction | Automatic (Focus, Astigmatism, Distortion) |
Data format | STL |
Power supply | 3-phase, 200 V (±10%), 35 kVA |
Weight | 4,900 kg |
Dimensions
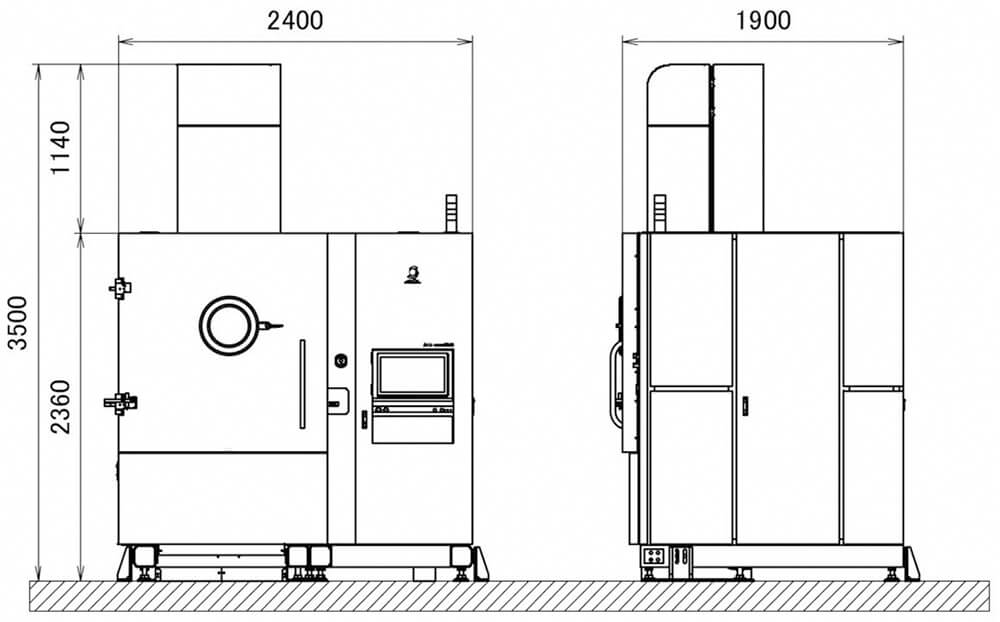
AM Samples
JAM-5200EBM
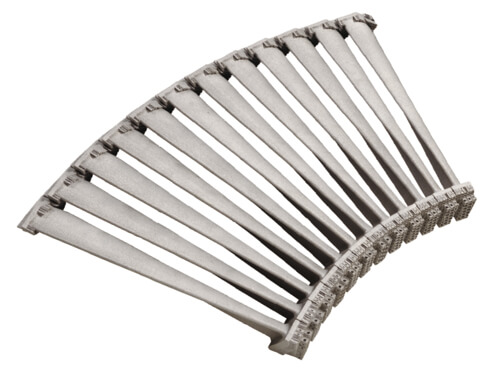
Low-pressure Turbine Blades for Jet Engine (Imitation)
Material: Ti-6Al-4V
Hight: 400 mm
12 pieces built simultaneously
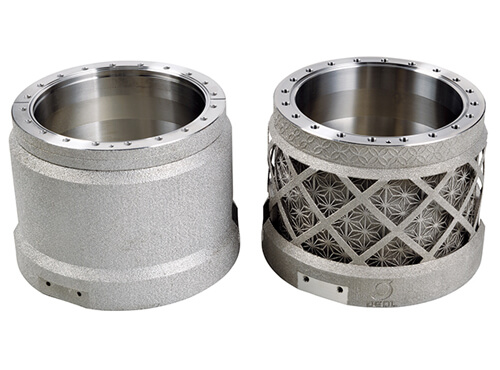
Electron Source Chamber
(Right side: approx. 25% weight reduction)
Material: Ti-6Al-4V
Each size: 230 mm (Dia.) × 185mm (Height)
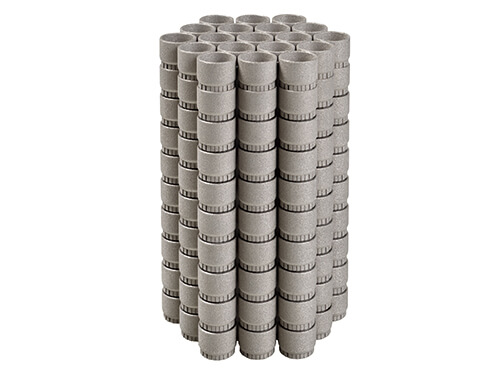
A small Sake Cup (190 pieces)
Material: Ti-6Al-4V
Height: 400 mm
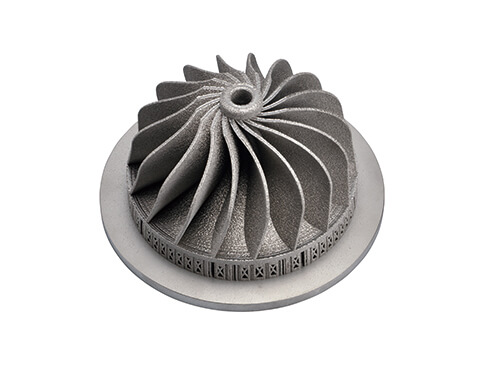
Impeller
Material: Ni-based Superalloy 718
Diameter: 170 mm
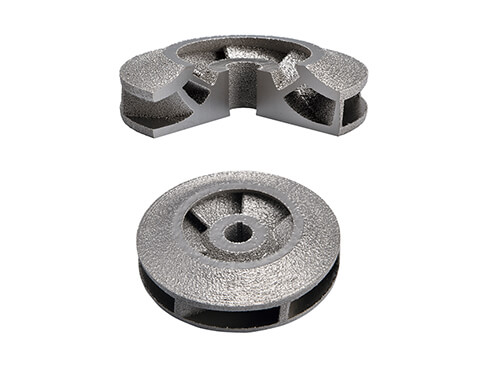
Closed Impeller
Material: Ni-based Superalloy 718
Diameter: 100 mm
Built horizontally without angles
CAD data: Courtesy of The Barnes Global Advisors
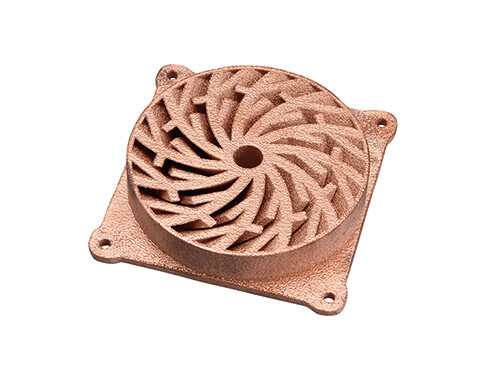
Heatsink
Material: Pure Copper
Size: 100 mm×100 mm
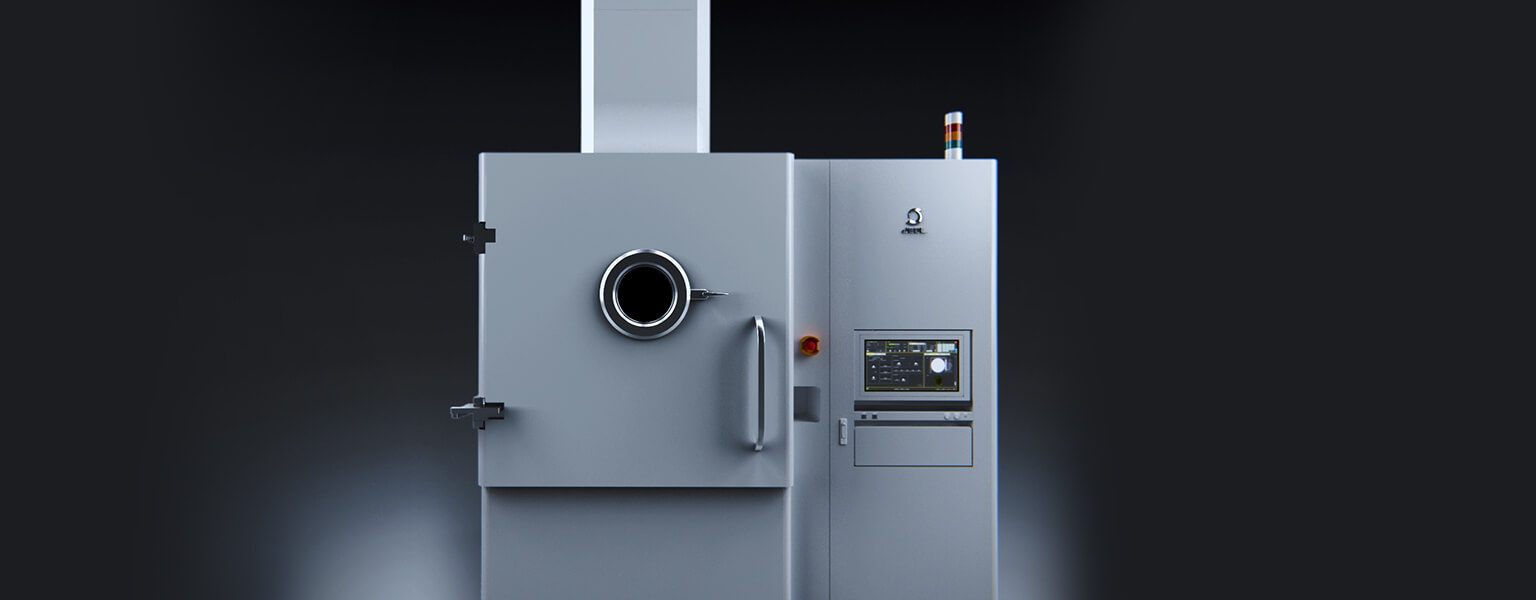
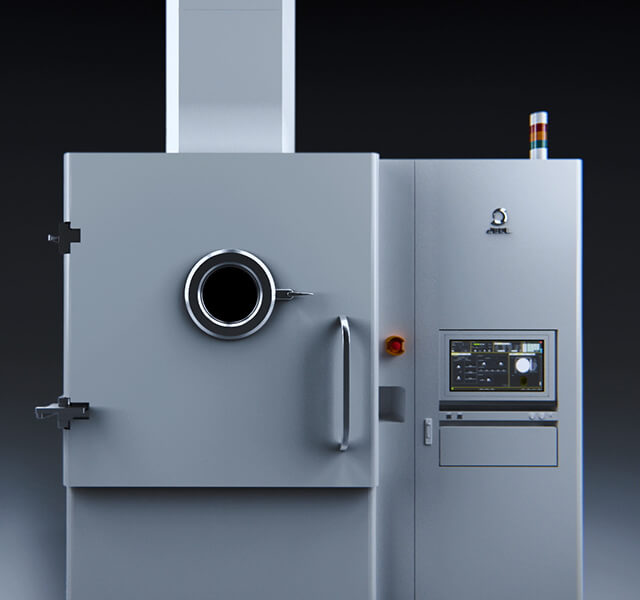
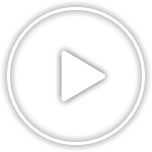
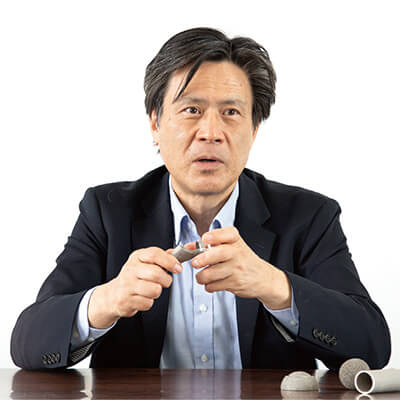
Revolution in material development by additive manufacturing using electron beam melting
-Departure from the legacy over thousands of years
Akihiko Chiba
Professor, Deformation Processing,Institute of Materials Research,Tohoku University
Additive manufacturing technology that uses AM Machine to produce metal parts. It is expected to revolutionize parts for aircraft and rockets, which require strength and reliability. We asked Professor Akihiko Chiba of the Institute for Materials Research at Tohoku University, who is leading the way in metal additive manufacturing technology in Japan, about the potential of this technology.
CONTACT US
If you have any questions or inquiries about "JAM-5200EBM" Electron Beam Metal AM Machine,
please contact us from below: